TECH TOPICS
技術トピックス
■注目の技術トピック
>> 銅バー(バスバー)における樹脂との接合
>> リチウムイオン電池(LIB)の構造とは
>> 自動車業界や産業用で使われる「防水コネクタ」の作り方とは
>> リチウムイオン電池(LIB)の電極部の気密性をあげるには
>> コネクタや自動車にも使われるバスバーの防水対策とは
>> インサート成形とインサート成形接合との違いとは?
2025.02.15
2025.02.17
工程を合理化する自動車・車載用「防水コネクタ」とは
自動車業界をはじめ、さまざまなモノづくりの現場において、工程の合理化はコストダウンや環境負荷の低減に繋がります。
「金属・樹脂 直接接合ラボ」を運営する睦月電機では、生産工程の効率化と品質向上を両立するために、新しい工法による「防水コネクタ」を提案しています。
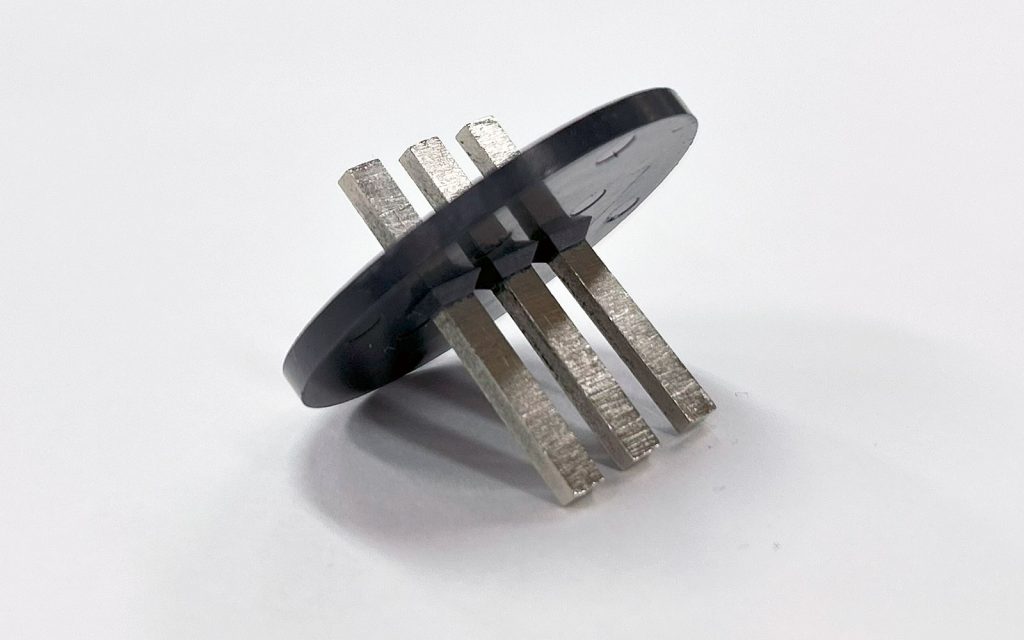
金属部材を金型にセットして樹脂と一体成型する、いわゆるインサート成形は、組立工数を削減でき、大量生産にも向いている生産性の高い技術です。
一般的にインサート成形で金属端子と樹脂と一体化するコネクタは、自動車・車載用にも数多く使用されています。
しかし、インサート成形では、金属と樹脂の界面は密着しておらず、わずかな隙間があるため、完全な気密性・防水性を確保しづらいことが最大の課題です。
自動車・車載部品は、気密の要求仕様が高いことが多いため、密着性の高いインサート成形技術が求められます。
完全封止が必要な場合は、後工程で接着剤を充填する、前工程で接着剤を塗布する、シール材を一次成形するなどの方法が施されています。
接着剤やシール材を使った封止の課題点
現在では、特殊な接着剤やシール材を使って密着性を向上させるインサート成形技術もでてきています。
しかし、金属と樹脂を接合するために、そのような副資材を使う場合は、下記のような課題も生じてきます。
◎接着剤の保管や工程管理が必要となる。
◎接着剤は経年劣化し、もともと水には弱いため、耐久性に課題がある。
◎廃番や気密性の許容範囲が変わった場合、新たな接着剤を選定する必要がある。
より効率的で工程を合理化する自動車・車載用「防水コネクタ」
「金属・樹脂 直接接合ラボ」では、独自のレーザー技術によって、金属端子と樹脂をダイレクトに接合し、防水性を確保する防水コネクタの製作が可能です。国内・海外で特許を取得したこのレーザー技術は、金属に特殊な凹凸形状を形成します。前工程でレーザーを照射し、射出成型。凹凸形状に隙間なく樹脂を入り込ませることによって、密着性を高めます。
この工法を「インサート成形接合」として提案しています。この工法は、自動車業界に求められる効率化やリードタイムの低減、部品点数の削減やコストダウン、環境負荷低減を実現し、防水コネクタといった完全封止が必要な部品の品質を向上します。
インサート成形接合のメリット
◎接着剤やシール材を使わないため…・材料を削減できます。
・材料の選定、保管や管理が不要です。
・接着剤の乾燥時間が不要でリードタイムを削減します。
・環境負荷を低減します。
◎独自のレーザー技術によって…
・タクトタイムを削減できます(照射時間は数秒~数十秒)。
・経年劣化を低減します。
つまり、金属部材と樹脂を直接接合するため、工程を合理化することが可能です。
インサート成形接合とは
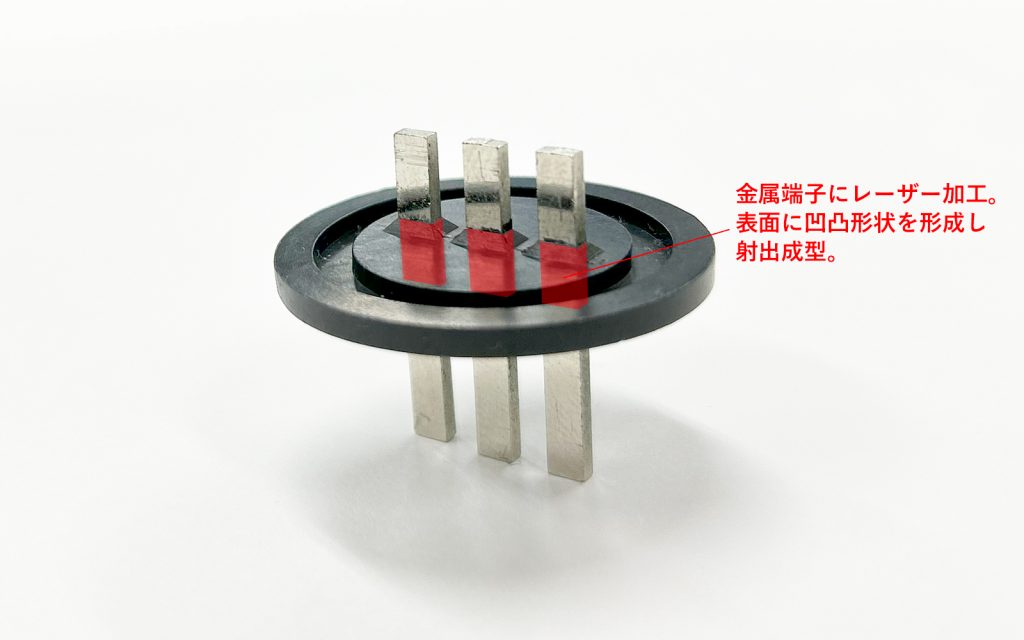
睦月電機は、自動車・車載用を主軸とした精密部品の樹脂成形を得意としており、プラスチックの可能性を押し広げることに挑戦しています。
その一環として、金属との直接接合を研究開発し、「ALTIM®」という技術を生み出しました。
この技術は、レーザーで金属表面に特殊な凹凸形状を形成することで、アンカー効果と樹脂の濡れ性を高めることができます。
こうした金属表面の凹凸形状に隙間なく樹脂を入り込ませるノウハウは、当社が長年培った射出成型技術にあります。
なお、「ALTIM®」とは射出成型だけでなく、切削品などの樹脂を後工程の加熱圧着によってピタッとくっつける技術です。
自動車・車載用「防水コネクタ」なら、当社にご相談ください。
「金属 樹脂 直接接合ラボ」では、独自の直接接合技術「ALTIM®」のレーザー技術を用いて、金属表面を粗面化し、射出成形時に金属表面と樹脂を密着させる「インサート成形接合」を提案しています。インサート成形だけでは担保しきれない強度、防水性、気密性を向上します。
自動車・車載用に限らず、コネクタの封止性能を高めたいお客様は、お気軽にご相談ください。